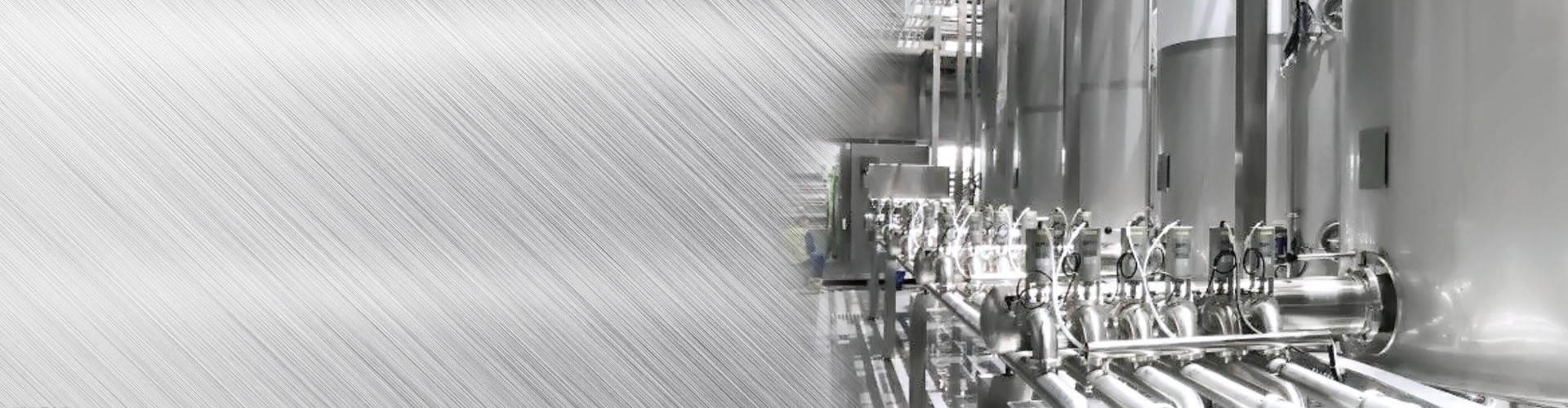
Many automatic production lines of "haohuan snail" constructed by BEYOND involve the processing and production of pickled products such as sour bamboo shoots, sour beans, agaric, dried radish and so on. This is a full-automatic production line of river snails rice noodle from food pretreatment to product packaging.
The pretreatment section adopts the feeding design, and the pretreatment part is set on the fourth floor. The materials are unpacked and unpacked in the pretreatment section, and the materials that are bad for some products are selected. The selected materials will be put on the third floor for further processing. This section is completely separated from the pretreatment workshop, which realizes that the materials in the pretreatment section and the pretreatment section are not mixed and the personnel are not flowing, and ensures the sanitary environment of the pretreatment section. In addition, the adoption of a million level purification workshop greatly reduces the breeding of microorganisms.
Pasteurization is adopted in the sterilization section, which uses lower temperature to kill microorganisms, while maintaining the flavor of nutrients in food. The equipment realizes full intelligent control, which is divided into feeding - sterilization - cooling - Cleaning - Drainage - air (drying) and other processes. The speed, time, temperature and other parameters of each section can be set according to the process formula to meet the actual production needs. The paperless recorder is used to record the sterilization time and temperature, and the historical data can be exported to realize periodic control, and different batches can realize dynamic sterilization. Keep the crisp taste of the product through rapid cooling, bag washing, water removal and drying. Ensure food safety, improve product quality and reduce labor.
CIP cleaning system is adopted in the cleaning section. After completing the production task, the equipment is automatically cleaned. Keep the equipment clean and eliminate the breeding of microorganisms in the equipment.
Clean after continuous production. The equipment is equipped with cleaning pipeline with automatic cleaning function. Equipped with return pump with self-priming function, there is no residual cleaning water in the equipment after cleaning. Make the equipment and production sanitary.
Adhering to the vision of "creating value for customers and leading the development of the industry", fully implement the six safety management concepts, do a good job in each production line with the mentality of "focus, concentration and professionalism", and work together with peers to create new brilliance in China's food machinery processing industry.